钢箱梁制造关键技术
发布日期:2020-03-20
钢箱梁为全焊接结构,结构复杂,熔透焊缝较多,从而导致焊接难度和焊后变形及焊接残余应力较大,使箱体制造难度加大。同时钢箱梁隔板采取了整体式隔板也给制造带来了一定的难度。实践表明:钢箱梁制造关键技术主要在于焊接质量、焊接变形及钢箱梁总拼控制。
钢箱梁焊接质量及焊接变形控制技术
主要焊接接头类型
钢箱梁主要焊接接头形式有对接接头和角接接头两种,即:U形肋与顶、底板的坡口角接,横隔板的立位对接,横隔板与顶板接板的横位对接,顶、底板的对接焊缝,顶板横向变坡自然坡口熔透角焊缝等。
主要焊缝焊接质量和变形控制技术
U形肋与顶板坡口角接焊缝的焊接和变形控制
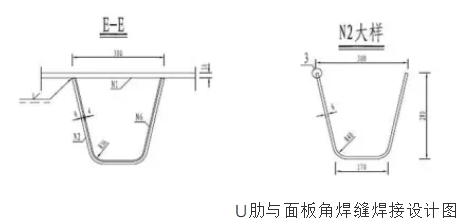
钢箱梁U形肋板厚8mm,要求焊缝有效厚度≥0.8倍的U形加劲肋的板厚,且不允许烧穿,并对焊缝进行磁粉探伤检测。
控制要点一:为保证焊缝的熔透率和减小焊接变形,通过焊接工艺评定试验,确定最优坡口形式、焊接参数,采用线能量较小药芯焊丝(φ1.6)CO2气体保护自动焊进行焊接。
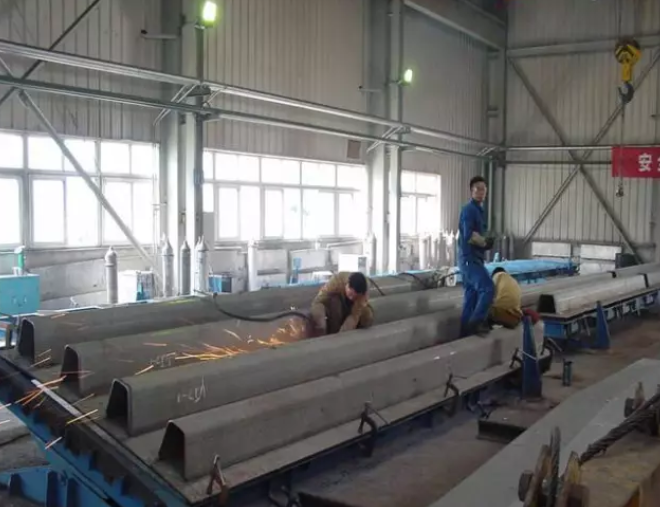
控制要点二:为控制板单元件在焊接过程中的横向收缩变形和保证U肋对焊接位置的要求,通过试验设计焊接反变形胎架,然后根据单元件变形趋势,总结变形规律,确定反变形量,使板单元在预拱状态下船位焊接,同时对顶、底板的自由边进行刚性固定,减小波浪变形。
控制要点三:板单元加工完成后,采用冷矫正或火焰矫正的方法,矫正单元件翘曲变形,重点矫正边缘的波浪变形,从而满足对接时平面度的要求。顶板单元件的纵向收缩变形采用3000KN液压矫正机进行冷压矫正。
控制要点四:整个板块采用同方向施焊,并采用合适的焊枪角度及焊丝送进位置。合理的焊接顺序可以减少不必要的焊接变形,能保证焊接质量和几何精度。合适的焊枪角度和焊丝位置可以保证坡口根部熔合良好及焊缝表面成型质量。
检测结果表明:采用上述工艺施焊的焊缝,焊缝有效厚度达到0.8-0.85倍U肋板厚,力学性能、抗弯性能、硬度等指标满足设计要求,接头断面无裂纹、气孔等缺陷。
顶、底板的对接采用实心焊丝CO2气体保护焊打底,埋弧自动焊填充盖面的单面焊双面成型技术。
控制要点一:为保证焊缝质量,通过焊接工艺评定试验,确定最优坡口形式、焊接参数和焊接材料。
控制要点二:通过对对接焊接收缩量进行测量跟踪、准确预留焊接收缩量,制作焊前板单元定位样板、焊后检查样板,充分保证焊缝两侧相邻U形肋的中心距,且预置反变形,以保证焊后板块的尺寸精度和平面度。
控制要点三:对单元件因运输或吊装等原因产生的变形进行矫正,后在单元合件拼焊胎架上,以纵横基准线为准,将两单元就位,确认对线无误、焊接间隙合理后,用卡兰将周边卡固。
控制要点四:由于拼接时,坡口间隙不匀易引起焊缝根部熔合不良,因此针对过大或过小的焊接间隙采用向前推或拉的运条方式及按线配切坡口来解决问题。
控制要点五:为避免由于打底焊道较薄,焊缝受热后易下坠而导致反面余高过高等外观不良等问题,要求焊接完第一道埋弧自动焊后再去除衬垫,让受热下坠的焊缝金属有所依托,同时,为减小焊接变形,马板应在打底焊道焊接完成后等温度降低后再拆除。
检测结果表明:采用上述工艺施焊的焊缝,焊缝力学性能、抗弯性能、硬度等指标满足设计要求,焊缝外观质量良好,对接质量合格。
横隔板对接焊缝的焊接与变形控制
目前国内钢箱梁横隔板形式主要有搭接、整体对接和整体横隔板三种,由于考虑到搭接会导致偏心,整体横隔板会造成仰焊,影响桥面板的耐久性,对整体受力性能不利,因此,大跨径悬索桥钢箱梁横隔板基本上采用上下两块或三块板组成的对接式横隔板,上下或上中下板块熔透对接,上板与顶板单元一起组装,板块间采用熔透对接方式相连。
控制要点:由于横隔板有几种规格,对于较薄横隔板的立位焊接,采用单面焊接双面成型,是一种可以保证焊接质量的方案,但当板厚较大时,改双面坡口可以减小焊接填充量,降低劳动强度,并减小了焊接收缩和焊接变形量。
控制要点:整体对接式横隔板在长度方向采用立位对接,宽度方向采用仰横位对接。立位和仰横位对接横隔板板厚为12mm的,采用单面焊双面成型,背面贴圆弧槽陶质衬垫。对于特殊梁段部分板厚为16mm的,考虑到单面焊接填充量大,焊接变形严重,所以立位对接采用双面V形坡口进行焊接。横位对接16mm厚板采用不对称K型坡口,先焊接大坡口侧,再反面清根焊接小坡口侧,保证熔透。
横隔板组装:横隔板是箱梁组装的内胎,它的精度直接影响着箱梁的断面尺寸精度。其由钢板、水平加劲板、竖向加劲板、人孔及管线孔加强圈组成。横隔板组装需保证平面度,板肋组焊采用线能量小的C02气体保护焊,焊后火焰调平。
横隔板组焊:从一端开始,依次按线组装横隔板,最后安装工艺隔板。组装过程中辅以定位夹具、顶拉工具控制隔板位置精度和垂直度等项点,使横隔板间距满足标准要求。先焊横隔板焊缝,再焊其它焊缝。
横隔板对接焊缝严格按照已评定的焊接工艺参数进行,焊接间隙保证在6mm左右,为保证背面成型质量,陶瓷衬垫必须烘干、贴紧,焊接完成后及时清渣,清除飞溅。
检测结果表明:采用上述工艺施焊的焊缝,焊缝力学性能、抗弯性能、硬度等指标满足设计要求,焊缝外观质量良好,对接质量合格。
顶板接板与横隔板横位对接控制
顶板接板与横隔板之间为融透焊缝,要求全部超声波探伤。此焊缝焊接形式困难,焊接量大,焊接变形大,对顶板高程影响大,为控制好顶板接板与横隔板横位对接必须采取相关控制措施。
控制要点一:接板与横隔板粗对位。
接板与顶板先进行整体组装,保证接板之间的距离与接板垂直度满足要求。在横隔板垂直度满足要求的前提下,在隔板上部两边点焊定位马板,使用插入式定位方法对接板纵向进行粗略定位。
控制要点二:保证接板与横隔板组装间隙。
接板与隔板之间组装间隙主要以顶板高程为准,并且兼顾接板与顶板间隙及焊接变形为原则进行精确定位。然后用马板将接板与隔板马固,进行焊接。
控制要点三:接板与横隔板焊接变形控制。
1)焊接工艺参数见2.2.3章节有关内容;
2)对接间隙控制,使其控制在6~8mm,对不满足要求的接板进行局部配切,以便于控制焊接变形及外观成型;
控制要点四:接板嵌补段组装。
接板嵌补段根据实际测量尺寸进行配切,用马板对接板进行精确定位后焊接;为减少接板焊接变形对隔板整体带来的影响,控制焊接顺序为:嵌补段先与接板两边焊接,再与顶板进行焊接,最后与隔板整体焊接。
横隔板单元件制作与整体组拼控制技术
横隔板是箱形梁组装的内胎,它的周边加工精度和U型肋槽口精度的控制是确保钢箱梁几何精度,顺利组装的关键。大跨径悬索桥钢箱梁宽度大,板单元间纵向对接缝较多,焊接变形对钢箱梁宽度影响较大。因此必须对隔板单元件制作和组拼进行控制。
横隔板单元件制作难点控制
钢箱梁隔板材质主要为δ10、12、16mmQ345C钢板,焊接收缩对隔板长度方向和平面度影响较大。如何保证隔板焊接完成后,焊接变形对单元件尺寸和U肋槽口尺寸以及隔板平面度的影响是隔板生产的最大难点。
控制要点一:对钢箱梁整体横隔板进行合理的分块。根据现场制造要求,将横隔板划分为三个单元件,中隔板、边隔板和角隔板。横隔板划分单元前,先在钢板上划纵横基线、托板位置线及机加工刨线。
控制要点二:单元件全部采用数控下料,先数控精切人孔、管线孔,最后切割周边,保证其制造精度。对单元件长度方向预留较为合适的工艺量并均匀分布于各个U肋槽口,保证槽口尺寸。
控制要点三:下料后对隔板进行预处理释放应力,尽量减少应力集中,有助于对接焊的应力变形。
控制要点四:对隔板板肋焊接顺序进行调整:中间→两边→四周。在板肋焊接前,先对线定位组装。
控制要点五:横隔板单元件焊接完成后,采用控制火焰温度和密集形梅花点进行火焰调直,保证单元件平面度。
钢箱梁板单元件的几何精度、焊缝外观及内在质量等均达到了《制造规则》的要求,可以满足现场钢箱梁整体组装的要求;钢箱梁制造过程中关键项点的控制措施得当,过程控制措施有力,其钢箱梁整体几何精度及预拼装精度达到了《制造规则》的要求;钢箱梁焊缝外观质量良好,内在质量优良,焊接试板所代表的焊缝力学性能均满足设计要求。
上一篇:波形钢腹板PC箱梁桥
下一篇:世界最大钢箱梁悬索桥横空出世!